What is a Cost Trade-off?
A cost trade-off refers to the decision-making process of choosing between two or more options that have varying costs associated with them. In essence, it is the trade-off between the costs and benefits of choosing one option over another. This concept is commonly used in business, engineering, and project management, where it is necessary to consider the impact of a decision on all relevant variables.
The interrelationship among system variables in a cost trade-off is crucial. In most systems, there are multiple variables that can be adjusted to achieve a desired outcome. For instance, in manufacturing, the production output can be increased by either adding more labor or investing in more advanced equipment. However, each of these options has different costs associated with it. Adding more labor may be cheaper initially, but it may increase costs in the long run due to training and management costs. On the other hand, investing in more advanced equipment may be expensive initially, but it may reduce costs in the long run by increasing efficiency and reducing the need for manual labor.
The decision to choose between the two options above involves a cost trade-off. If the goal is to reduce costs in the short term, adding more labor may be the preferred option. However, if the goal is to reduce costs in the long term, investing in more advanced equipment may be the better choice. The decision-making process becomes even more complex when there are multiple variables involved, and a change in one variable affects the costs of others.
For example, reducing the size of a product may reduce its manufacturing costs but may increase packaging costs. Similarly, reducing the number of features in a product may reduce its manufacturing costs but may decrease its market value, leading to lower sales revenue. These trade-offs require careful consideration of all relevant variables and their associated costs.
What is Total Logistics Costs Trade-off?
Total logistics costs consider the whole range of costs associated with logistics, including transport and warehousing costs and inventory carrying, administration, and order processing costs. Administration and order processing costs are relative to the total volume being handled. However, for the same volume being handled, transport and warehousing costs will vary according to the adopted distribution strategies.
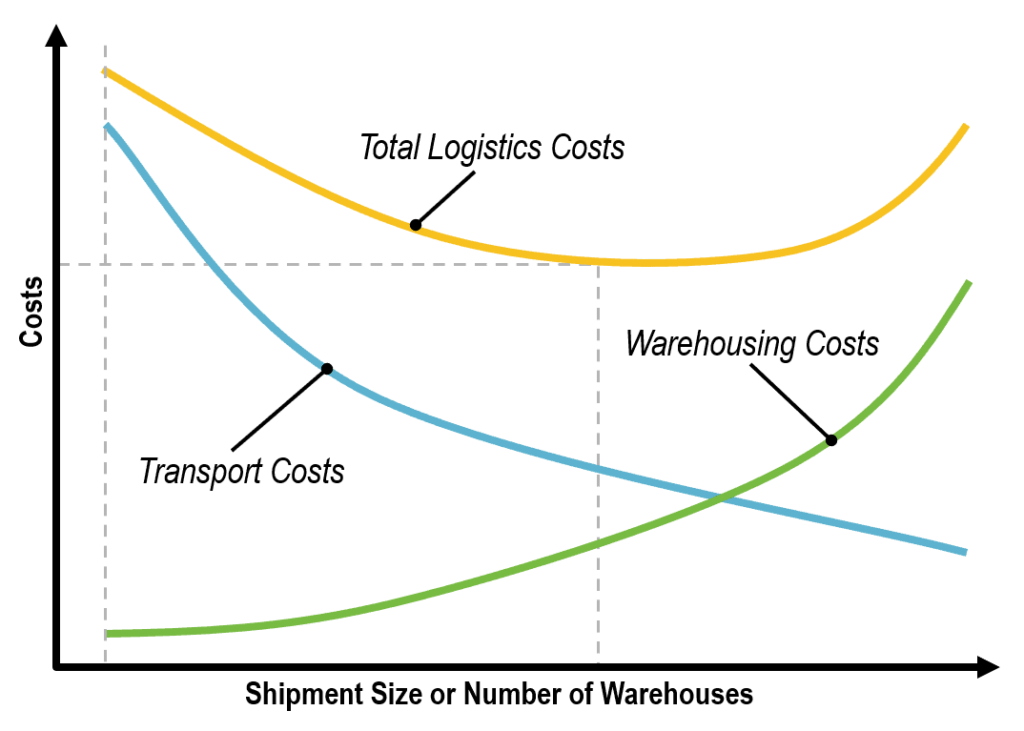
The above graph portrays a simple relationship between total logistics costs and two important cost components; transport and warehousing. Based upon the growth in the shipment size (economies of scale) or the number of warehouses (lower distances), a balancing act takes place between transport costs and warehousing (inventory carrying) costs. There is a cutting point representing the lowest total logistics costs, implying an optimal shipment size or number of warehouses for a specific freight distribution system. Finding such a balance is a common goal in logistical operations. It depends on numerous factors, such as if the good is perishable, the required lead time, and the market density